25 Jul How does processing affect pellet quality?
M. Verhoeven MSc (Zetadec, the Netherlands) and Dr. M. Thomas (Zetadec, the Netherlands and Wageningen university)
In a previous article, we have seen that physical pellet quality is dependent on the component composition of raw materials used in the formulation. The next question to ask is which other factors affect pellet quality. How do pelletizing processes and their conditions affect physical pellet quality?
Feed processing is not a single-step operation; it is a cascade of operations, each influencing the process in different ways. Pellet quality is proportionally dependent on diet formulation (40%), particle size (20%), conditioning (20%), die specifications (15%) and cooling and drying (5%), implying that 60% of the final pellet quality is determined during the different process operations of feed processing. The current article distinguishes the effects of milling, pelletizing and cooling on physical pellet quality.
Milling
The first operation in feed processing is milling. During milling (also referred to as grinding) a force is applied to an ingredient, breaking bonds in the feed material and reducing the particle size. A beneficial result of reduced particle sizes is the increase in available surface of the particles for binding during pelleting. Moreover, materials which are ground well are known to result in homogeneous mixtures; homogeneity is a desirable characteristic for a feed mash.
Commonly used parameters used to evaluate milling effectiveness are particle size distribution (PSD) or geometric mean diameter (GMD). However, how do we arrive at an optimal PSD or GMD? The type of mill used, and its operational variables are known to greatly affect the degree of particle size reduction of raw materials. The two conventionally most used types of mills in feed manufacturing are the roller mill and the hammer mill, of which the latter will be discussed in this article.
Important processing variables for hammer mills are hammer tip speed and hammer mill screen size. As can be seen in Figure 1a, an increase in hammer tip speed contributes to a higher particle size reduction and thus a relatively fine mash. With an increase in hammer tip speed, the particles will follow a pathway closer to the screen due to the centrifugal force. Figure 1a illustrates that the smaller particles can leave the screen under a relatively wider range of angles as compared to the more coarse particles. Figure 1b shows that an increase in hammer mill screen thickness will also result in a relatively finer mash, as the coarser particles can only pass through the screen under a relatively narrow range of angles.
After leaving the mill, the ground raw materials are mixed and transported towards the conditioner which incorporates heat and water (most often in the form of steam) into the feed mash. The impact of steam on pellet quality is described in the article of Duitshof and Thomas and will therefore not be discussed in the current article.
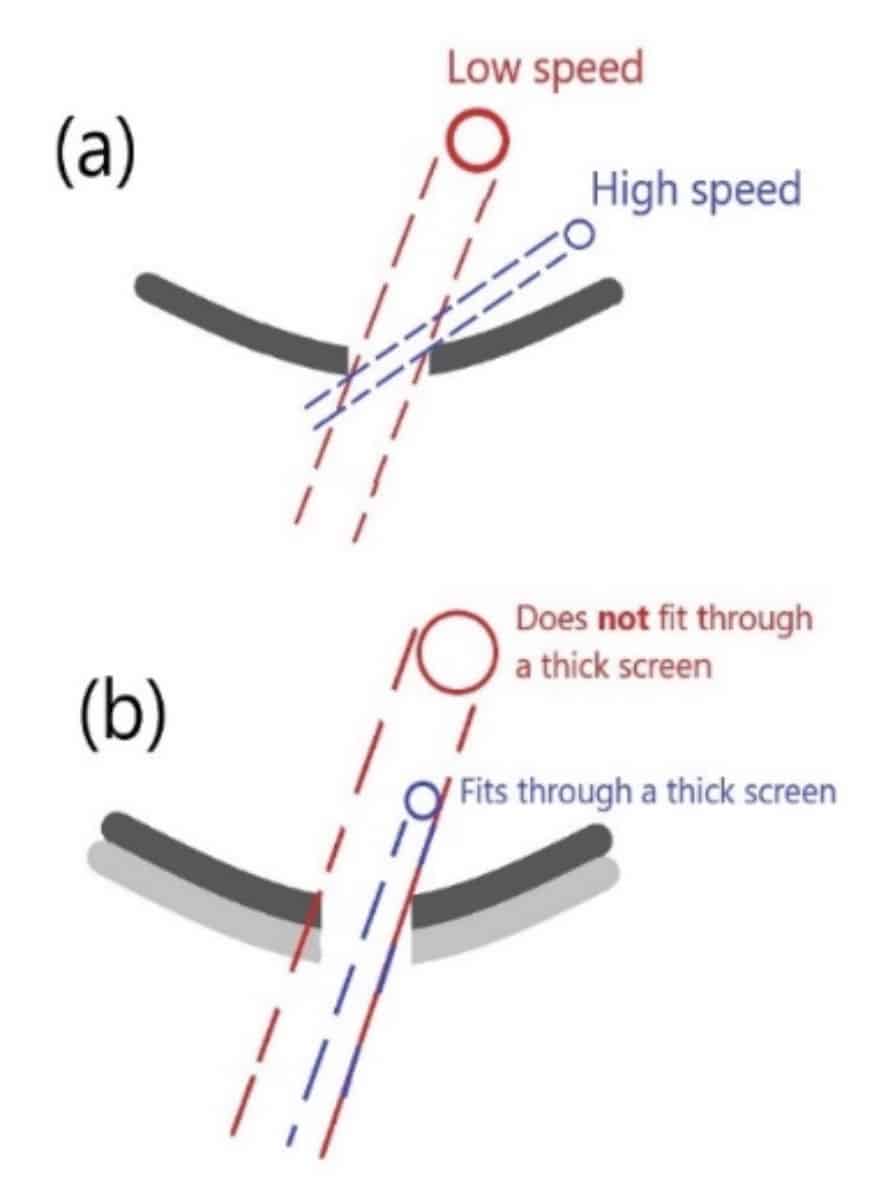
Pelletizing
The next step is the creation/formation of the pellets. Pellets or kibbles are either formed during a pelletizing or an extrusion process, respectively; the current article will focus on the effects of processing parameters during pelletizing on the physical quality of the feed.
The length:diameter ratio (L/D ratio) of the die holes is one parameter that greatly influences the pellet quality. Suppose we have two dies, both having die holes of 6 mm diameter. The length of the holes of the first die being 36 mm (L/D ratio of 6), and the length of the holes of the second die being 60 mm (L/D ratio of 10). The latter die is a thicker die and will generally result in improved pellet quality as compared to the thinner die. This increase in pellet quality with an increase in L/D ratio, can be explained by the larger amount of shear encountered in the thicker die. As the material remains longer in the compressed state, relaxation of stresses in the material will cause the role of the elastic components in the feed to decrease. With the contact surface between the feed mash and the die hole increasing, frictional forces increase and binding between particles is enhanced. Common L/D ratios in the production of livestock feed range from 8 to 12. Lower L/D ratios might result in higher production rates, but pellet quality is likely to suffer.
Next to the L/D ratio, the distance between the roller and the die, referred to as the gap-size, is an important parameter in pelletizing, and has an estimated optimum of 2-2.5mm. The increase in pellet quality with an increase in gap-size up to 2 mm is explained by the principle of compaction. The larger the gap-size, the thicker the layer of feed mash located in between the roller and the die and the more compacted and de-airated the mash will be before entering the die hole. This results in the feed mash entering the die hole under higher pressure, leading to better compacted particles and thus feed pellets with better physical properties. Upon increasing the gap-size further than 2 mm, durability drops, energy consumption increases and chances arise that the pelletizer will block. This further increase in distance leads to a decreased stability of the feed mash on the edge of the roller and die, resulting in feed mash “leaking” sideways from the rollers. Increasing gap-size beyond 2 mm should always be done with caution.
Cooling
Even though the process of pelletizing seems to be finished after leaving the die, the subsequent cooling and drying are important last steps in obtaining an optimal pellet quality. Pellets leaving the die generally have a temperature between 60 and 95°C with moisture contents ranging from 120 to 175 g/kg. Decreasing the moisture content makes it possible to store the feed for a longer time. The drying stage also helps to create bonds between feed particles due to recrystallization of soluble components in the feed. Cooling will result in increased viscosity of some feed components and thus in maintaining the structural integrity of the pellets. Air-flow, air-properties, raw material characteristics and pellet size are the main factors affecting the amount of water and heat that is dissipated from the pellets. For efficient cooling, the airflow should pass evenly through the bed of pellets, to prevent pellets with uneven moisture contents. Even airflow in coolers is obtained by assuring that the bed height of the pellets is close to spirit level along the cooler surface. The ideal bed height should be as such, that the mean residence time is between 15 and 20 minutes, which seems to result in optimal physical pellet quality. Other important factors in cooling are the diameter and initial temperature of the pellets entering the cooler: warmer pellets with a larger diameter have lower cooling rates as compared to relatively colder and pellets with a smaller diameter. In practice, feed manufacturers should aim to apply an optimum air speed for the pellet diameter produced. The Reynolds number is often used to obtain the optimal air speed in a cooler. This number is a dimensionless figure which is calculated from the air speed in meters per second, pellet diameter in meters and viscosity of the air, as is shown in Equation 1. The value of 1.82 * 10-5 m2/second is used in practice for the viscosity of air.
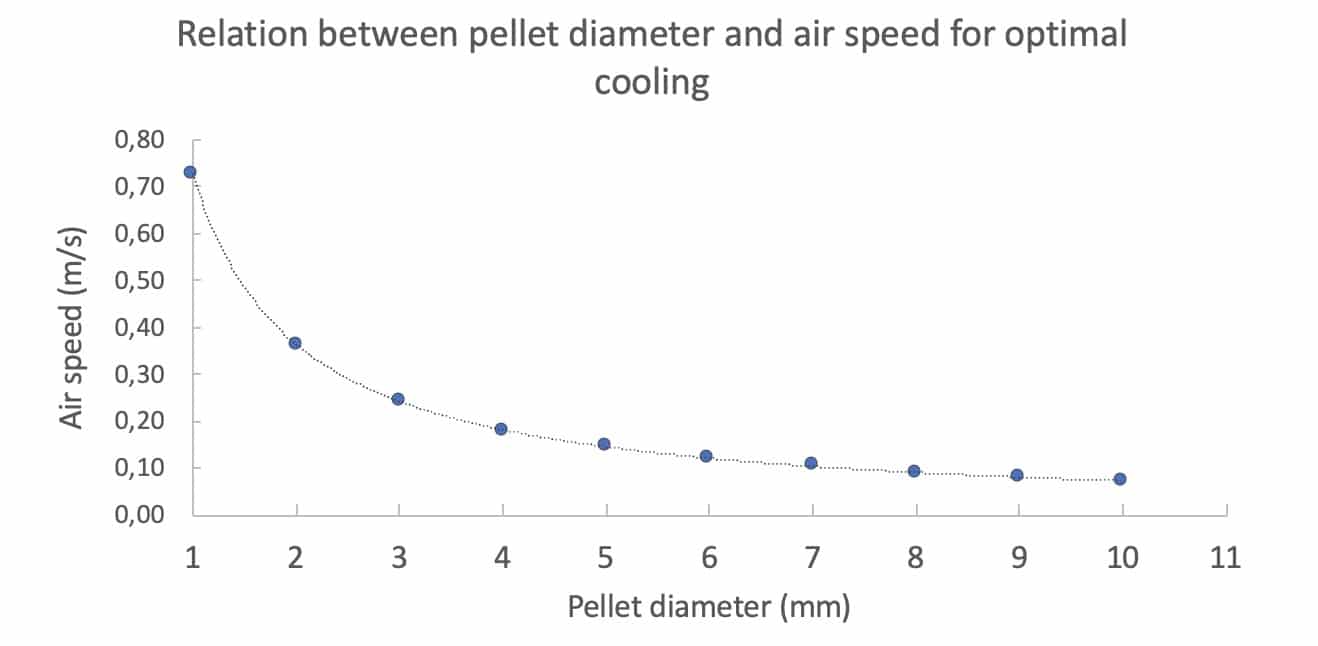
Figure 2 shows that an increase in pellet diameter requires a decrease in overall air speed in the cooler. Increasing the air-speeds in the cooler above the optimum negatively affects pellet quality because the outer layer of the pellet is drying at such a high rate that stresses are induced in the pellet. This might result in cracks emerging at the surface of the pellets, making the pellets more vulnerable to abrasion. Too low an air speed leads to insufficient evaporation of water and removal of heat, which is not desired either.
Conclusion
Feed manufacturing is a cascade of events, ultimately resulting in the animal’s diet: pellets. The final quality is dependent on the combination of all processes, from diet formulation up to cooling of the pellets. Optimal process conditions are dependent on multiple factors ranging from the components that are incorporated in the feed formulation up to the desired physical pellet parameters. The ultimate goal is to optimize each process individually and combine all processes as such, that the best results in terms of pellet quality are achieved.
References available upon request.
Sorry, the comment form is closed at this time.