25 Jul The effect of conditioning on pellet quality
S. Duitshof MSc (Zetadec, the Netherlands) and Dr. M. Thomas (Zetadec, the Netherlands and Wageningen university)
One of the factors affecting the structural quality of pelleted feed is the conditioning process. During conditioning the feed mash is softened and heated in preparation for pelleting. During conditioning, steam quality, temperature, residence time and type of conditioner have the most influence on pellet quality.
Steam quality
The first and foremost factor affecting pellet quality is the steam quality. Keeping the steam quality in check is difficult because of the many factors affecting the quality of the steam. This paragraph will provide an overview on the role of steam during conditioning, how to recognize good quality steam and what measures can be taken to improve steam quality.
Steam is used during conditioning to increase the temperature and moisture content of the feed mash. Because of its gaseous state, steam can spread uniformly over the feed mash in the conditioner. High quality steam has sensible and latent heat. The sensible heat present in the steam is the first to heat the feed particles, after which during condensation of the steam the feed particles are further heated with the latent heat. The moisture present in the steam has two main roles, it moisturizes the outer layer of the feed particles which aids in the formation of bonds between particles, and, in combination with heat, it alters feed components, such as the gelatinization of starch granules (Thomas et al., 1997).
The use of poor-quality steam, also referred to as wet steam, negatively affects pellet quality. Wet steam forms when the steam pressure and temperature are in a range that allows water condensate to form and mix with the steam (see figure 1). Because wet steam is less efficient in heating feed mash, more steam is required and excess water is added to the feed mash. This excess water tends to over-lubricate the feed mash, leading to pelletizer blockage.
Obtaining high quality steam is commonly done by placing a pressure reductions system close to the conditioner, placing sufficient water traps in the steam supply line leading to the pressure reduction system and keeping all steam pipes properly insulated (Campabadal and Maier, n.d.). The water traps remove excess water from the steam supply and, by reducing the steam pressure, the small amount of water still present in the steam is evaporated and good quality/slightly super-heated steam can be created. For instance: high quality steam at a pressure of 8 bar will have a temperature of approximately 170°C and contains 2768 kJ/kg. After reducing the pressure to 2 bar the temperature will drop to approximately 120°C and the steam will contain 2706 kJ/kg of energy (Figure 1). The difference in energy between the high and lower pressured steam is 62 kJ/kg, this energy is available directly after pressure reduction to evaporate any water present in the steam or if no water is present to increase the steam temperature and produce “super-heated” steam.
Good quality steam can be recognized as it is invisible when it exits the steam lines because all water has been evaporated. Only several (10-20) centimeters from the exit of the steam pipe (for example if you open the valve -if available- at the low pressure side of the steam pressures reduction station) the steam will become visible at a certain point due to the loss of temperature and condensation of the water vapor into visible droplets. Another method to recognize good quality steam is to measure the temperature and water content of the feed mash before and after conditioning. The relation between increase in water content and temperature provides insight in the quality of the steam. As a rule of thumb, we can say that good quality steam will increase the temperature of the feed mash by 16°C for each percent of moisture added to the it.
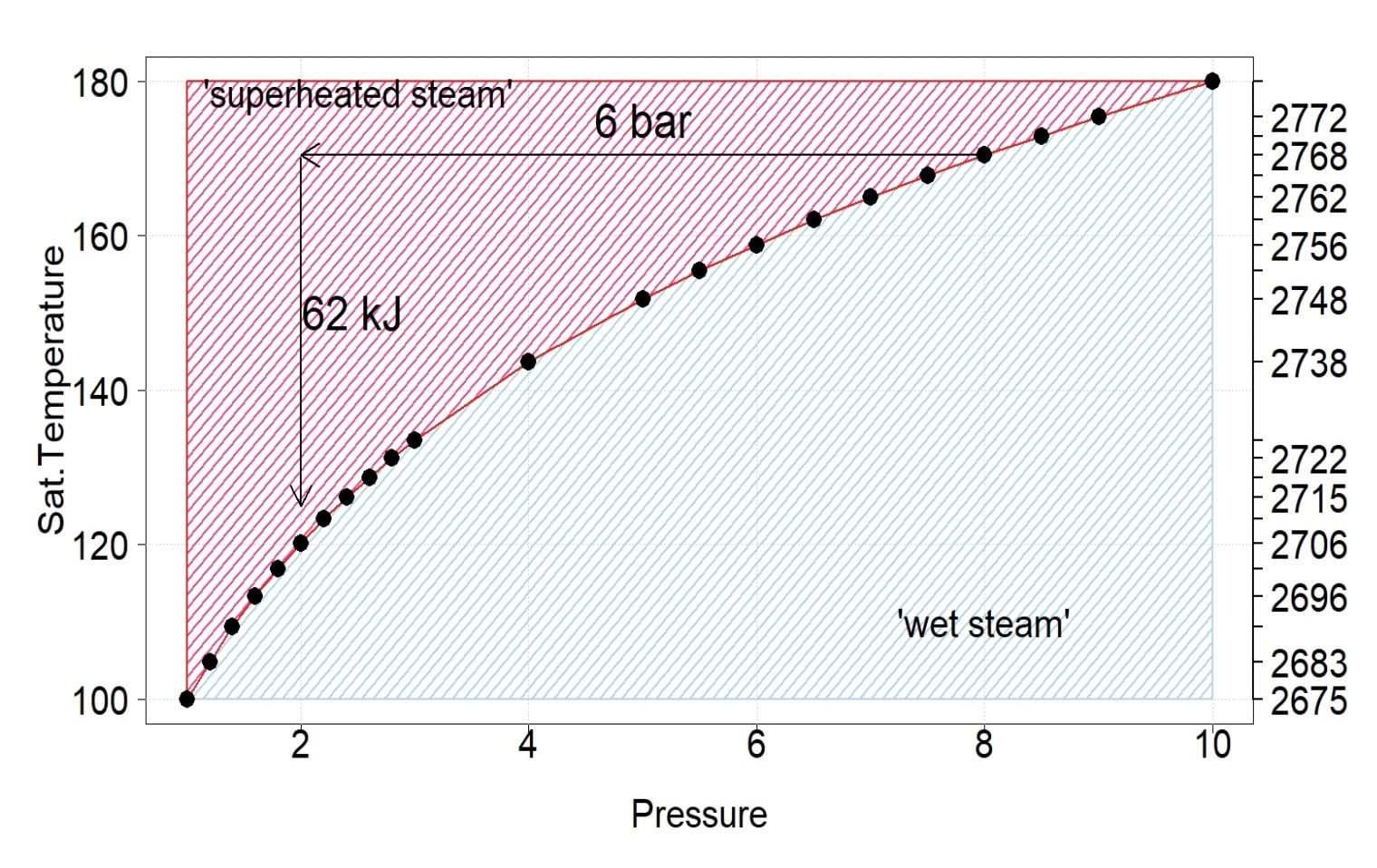
When good quality steam is achieved, the optimum steam pressure and temperature that should be added into the conditioner depend on the feed being produced. The following table provides a brief overview of steam values for different types of formulations.
Table 1. Steam conditioning recommendations from different diets (Thomas et al., 1997)
The practical implications of Table 1 are: when using low pressure steam more water is added to the feed mash compared to when high pressure steam is used, for the same amount of added heat.
Temperature
After good quality steam is achieved, the next factor that can increase pellet quality is the conditioning temperature. This temperature is increased by adding more steam into the conditioner, which as a side effect will also increase the water content of the feed mash.
The combination of increasing temperature and moisture content affects the plasticity of polymer feed components such as starch. These components can be present in different physical states (Keetels, 1995).
- a solid brittle phase (glass+ crystalline)
- a solid plastic phase (Amorphous + crystalline)
- a liquid or ‘molten’ state.
Native starch present in feed mash consists of a large proportion of crystalline particles and a small amount of amorphous particles. Starch high in amorphous particles and low in crystalline particles is known as pre-gelatinized starch.
The relation between the three states, temperature and moisture content can be seen in a state phase diagram such as Figure 2. In this figure two curves are visible: The lower curve is the glass transition curve (Tg), the second curve is the melt transition curve (Tm). The crystalline material will only change when the process conditions cross the Tm, after which the crystalline structures will be broken down. During cooling and moving back through the Tm and Tg, these particles will not become crystalline again but remain amorph. Amorphous particles become soft and pliable after conditions cross the lower Tg.
Particles in the glass stage can hardly form bonds with other particles while particles in the amorphous stage are able to bond with other particles, because they are soft and compactable and the amorphous viscous material can form bonds at the contacting points. In order to get strong pellets, it is important to promote particle-particle bonding (Thomas, 1996). Thus, the conditioning temperature & moisture content should be in a range that most particles have become amorphous and are easy pliable.
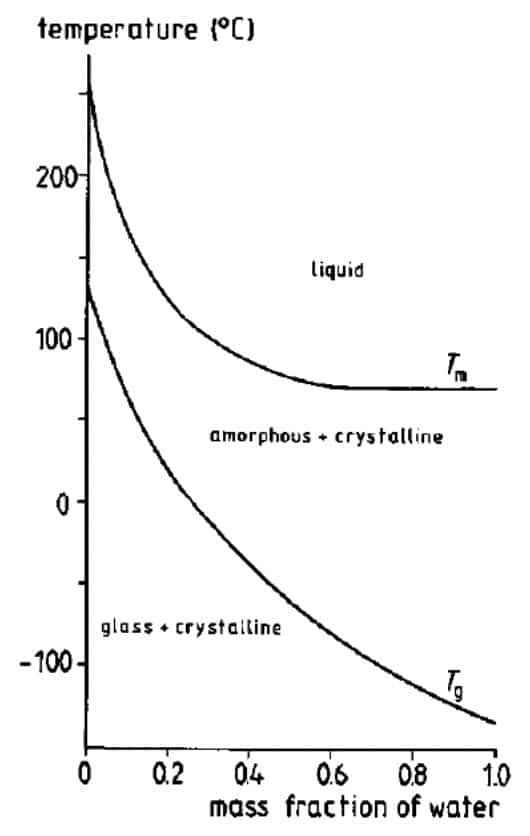
Literature sources are not clear in the effect of temperature on pellet quality. Loar et al., 2014, Teixeira Netto et al., 2019 and Cutlip., 2008 found that increasing the conditioning temperature increases pellet quality, while Rigby et al., did not find an effect of conditioning temperature on pellet quality. These conflicting results could be due to differences in moisture addition when changing conditioning temperature.
Besides the effect on pellet quality, increasing the temperature has a large effect on the nutritional value of the produced feed. At higher temperatures some of the nutritional value can be lost due to degradation of heat sensitive components e.g. Vitamins and maillard reactions. Be aware that the addition of poor-quality steam can lead to excess water added to the feed mash which could lead to pelletizer blockages and thus result in not being able to reach the desired temperature.
Residence time
Another factor influencing pellet quality is the residence time of the feed mash in the conditioner. Within a conditioner, residence time is normally altered by changing the level of fill. Normally this is done by changing the angle of the paddles on the mixer shaft. Feed mash that is kept in the conditioner for a prolonged time normally has an increase in pellet durability (Huang et al.,2014).
Moisture diffusion into the feed particles is a relatively slow process compared to the diffusion of heat (Guerin., 2019). Therefore, particles that have been conditioned longer are less brittle and more plastic compared to particles with a shorter conditioning period, where the interior of the particle is still dry and brittle. More plastic particles result in better compaction of the particles to pellets. If sufficient moisture is still at the outside of the feed mash particles during pelletizing, binding is improved. Over conditioning leads to soft, pliable particles but lacks formation of bonds between particles due to absence of liquid bridges (Thomas et al., 1996). Liquid bridges are easy to form, weak bonds between particles. During cooling of the pellets these liquid bridges are transformed into strong solid bridges due to the removal of moisture from the pellets during which solid material is deposited at the contacting points and builds a strong bond between feed mash particles. This leads to a stronger pellet.
High pressure conditioning
In modern feed mills, besides normal conditioning high pressure conditioning is performed. Most commonly an expander, double pelleting or a BOA compactor is used in this process. High pressure conditioning uses mechanical energy to exert shear and increase the density of the feed mash, thus altering the structure. These changes in structure increase particle binding and decrease pellet porosity after pelleting which also results in higher quality pellets (Thomas et al., 1996). Additional effects of high-pressure conditioning are a further decrease in the size of the feed mash particles and decreasing the energy consumed of the pellet press. However, the total energy consumption for feed production including the expander, boa or the additional pelletizer will increase, usually by about 15%.
Take home messages
Conditioning is an important factor in creating good quality pellets. Optimizing pellet quality by altering conditioning parameters can be done by: making sure the steam is of high quality, increasing the temperature of the feed mash, prolonging the residence time in the conditioner and/or adding high pressure conditioning to the pelleting line.
Frequently checking the quality of the steam added into the conditioner is important. These checks encompass the whole steam delivery system, boiler functioning, effectiveness of the steam traps, the pressure drop over the steam reduction system and finally a visual check of the steam added to the conditioner.
There are several situations in which increasing conditioning temperature is beneficial: the current conditioning temperature is low, the steam is of a good quality, and the nutrients in the feed mash are not affected by degradation due to the higher temperature. The increased temperature plasticizes polymer feed components such as starch and protein which will improve pellet quality, increase capacity and reduce specific energy consumption.
Increasing the residence time of the feed mash in the conditioner affects the position of water in the feed mash particles. This in turn may lead to better plastication which may improve pellet quality. Too short a residence time will lead to excess moisture at the outside of the particle; this will lead to blockage of the pelletizer. Optimizing residence time to match particle size is therefore relevant to obtain the best possible pellet quality.
High pressure conditioning will increase pellet quality at the expense of increasing the mechanical energy used in the production process.
References available upon request.
Sorry, the comment form is closed at this time.