26 Sep Thermomechanical treatment of feed during the pelleting process
Comparison of industrial lines with a pilot line
Author: Sandy Rouchouse, Tecaliman
This article is a follow-up to a previous paper which described the pelleting process used in animal feed plants and, more specifically, the heating phenomenon observed in the die as the feed passes through it during this process.
In this paper, we will present an example of a pilot press and compare how feed behaves in the press of this pilot tool with how it behaves in an industrial press. The main advantages of this type of tool are its ability to process feed in small batches and its full instrumentation. It is also important for it to be representative of industrial pelleting lines.
Description of a pilot pelleting line
Pilot pelleting lines can have different objectives, for example to test the ability of a new raw material to be pelleted, or to evaluate how pelleting affects the nutritional value of a formula or additives’ resistance to the process. Tests are run on pilot tools since processing small batches makes it possible to limit the costs of these tests and to increase the number of parameters tested in a single day (up to 6 tests per hour).
An example of a pilot pelleting line is shown in Figure 1. This line is like an industrial line in that it comprises a hopper, a screw feeder, a conditioner equipped with a temperature sensor and a steam control loop and, finally, a pelleting press with a die and rollers used to shape the pellets. The press has a 3 kW motor (compared to 200 to 250 kW for most industrial presses) and the flow rates used are generally between 30 kg/h and 100 kg/h (compared to 3t/h to 20t/h in a plant).
Not only does the press have different dimensions, but it also has a different pellet shaping mechanism. Unlike the rotary ring die presses generally found in animal feed plants, the press presented in this article is equipped with a flat die and two rollers rotated by the press motor (Fig.2). Rotary knives cut the pellets to the desired length. Because the die is fixed, it was possible to drill a hole in the steel to insert a thermocouple connected to a data logger. This allows the die temperature to be recorded every second, in addition to the conditioner outlet temperature, press power, etc. This line is therefore capable of communicating and recording the maximum temperature to which the feed is subjected, which is an important parameter in explaining the behaviour of a product or of an additive during the process. Finally, a cooler-dryer equipped with a 7l bin dries and cools the pellets produced.
The flexibility and instrumentation of this pilot pelleting line make it a real alternative to industrial testing, which is often time-consuming, hard to implement and involves parameters that are not easily controlled. The question is: how does the validity of tests carried out using this press compare with that of tests carried out on an industrial line? Which scaling factor should be used? The second part of this article will address these questions.
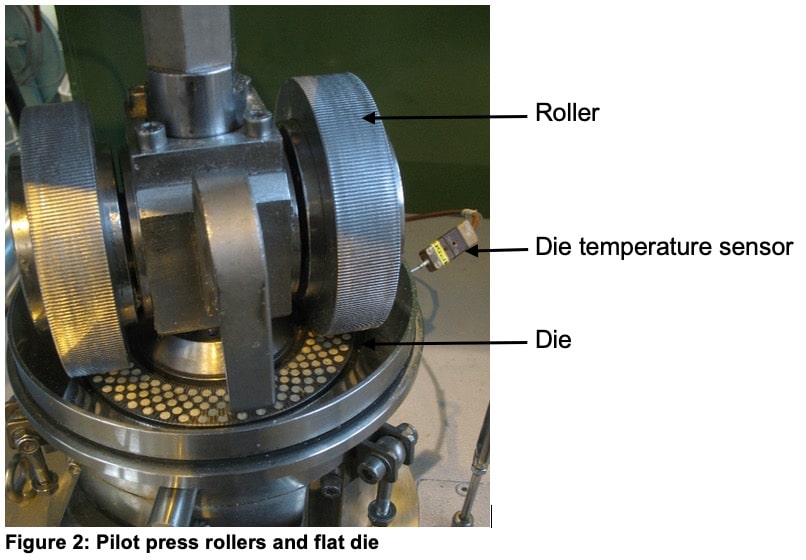
Scale transfers between a pilot line and an industrial line
Several parameters can be used to determine how representative a pilot line is of an industrial line: the physical quality of the pellets produced; the temperature that feed is subjected to in the die; and, finally, the length of time that feed is exposed to the maximum temperature (time spent in the die).
Figure 3 illustrates the temperature pig feed is subjected to when in the die during production on eight different industrial lines (blue dots) and in the pilot press described above. The graph shows the different dies used in the pilot press for pelleting (yellow dots for die 1; orange dots for die 2; red dots for die 3). The graph demonstrates that, when the appropriate die is chosen, the temperatures reached in the pilot press die are consistent with those observed in a plant.
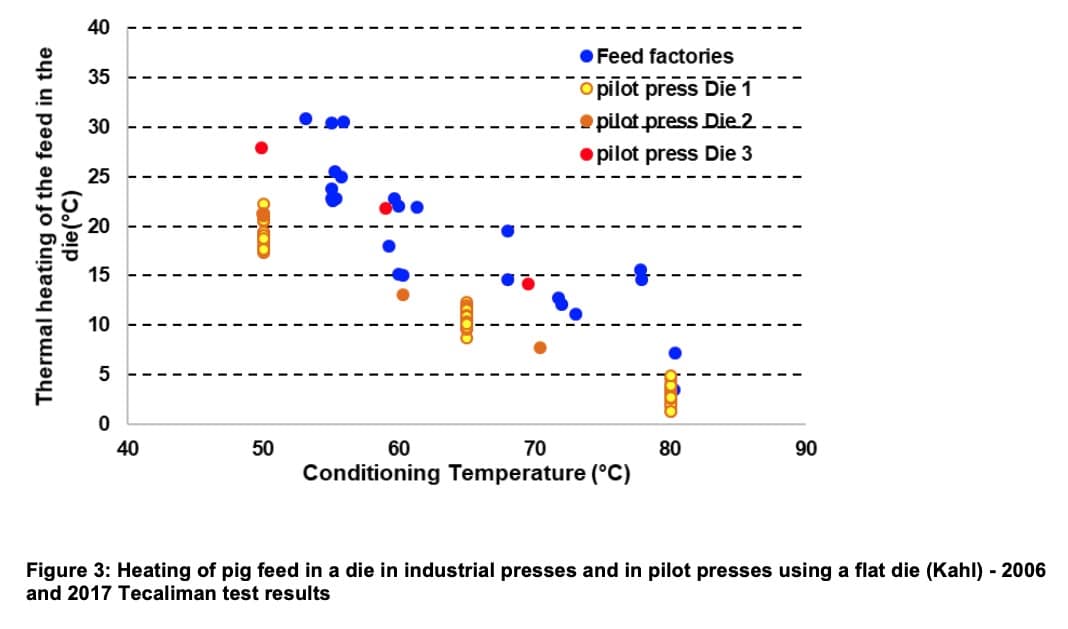
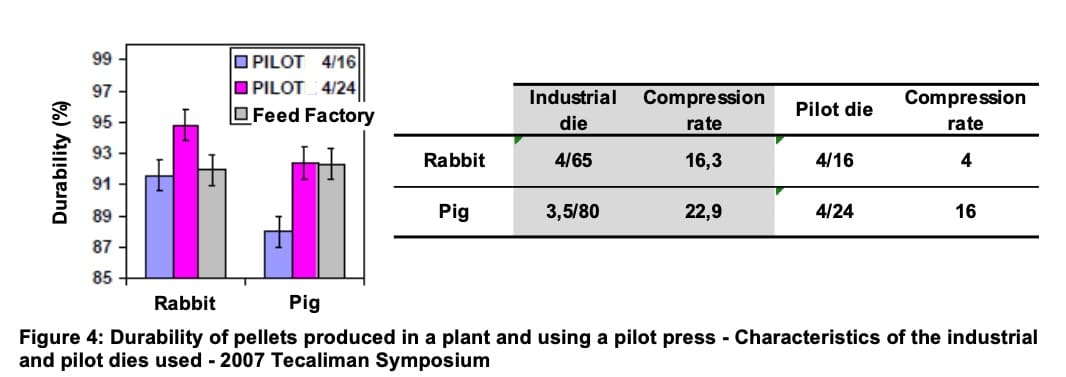
The tests shown in Figure 4 involved use of the same feed formulas in both the pilot press and the industrial press. The durability of the pellets produced was also measured. These measurements can be used to evaluate the pellets’ resistance to shocks and abrasion, which is the main indicator of physical pellet quality. A pellet with a durability close to 100% has good cohesion and is “shock resistant”.
For rabbit feed, the durability obtained with the 4/16 pilot die is the same as that obtained with the industrial press. For pig feed, the 4/24 die seems more appropriate. The compression rate, equal to the ratio between the length of the holes and their diameter, indicates that a factor of 4 between the industrial and pilot dies is required to obtain the same product quality. Here too, if the die is well chosen, the pilot press can produce pellets that have the same texture as that observed at a plant.
Finally, we were able to measure the length of time that the feed remained in the die by taking into account the pellet mass in the die and the instantaneous flow rate of the pellets. Tests carried out at 8 industrial sites pelleting pig feed show that the time spent in the die varies between 2.5 seconds and 13.1 seconds. For chicken feed, the time spent in the die ranges between 1.9 seconds and 9.8 seconds. In the tests carried out using the pilot press, the feed remained in the die between 3 seconds and 9 seconds, thus covering a wide range of times observed in plants.
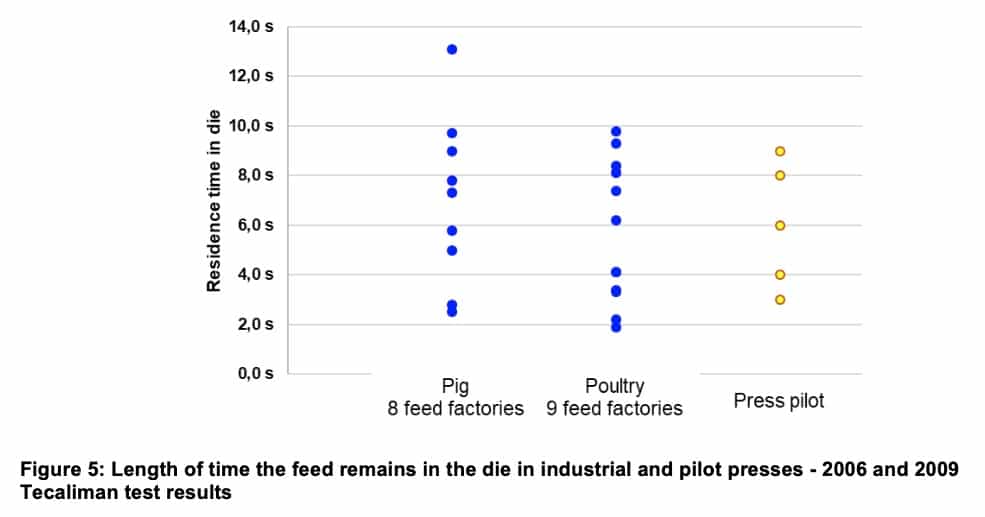
Conclusion
The feed pelleting process is characterized by a time/temperature combination that pellets are subjected to while they are being shaped. Although the pilot press described in this article uses a slightly different technology to that used in plants, it was able to respect the combinations observed in plants and the pellets produced were of the same physical quality as industrial pellets. This pilot line, developed by Tecaliman, the French technical centre for animal feed, is currently being used for R&D purposes by additive manufacturers who want to know how well their product resists the pelleting process. It is also used to evaluate whether or not a new raw material can be pelleted. It is therefore a viable alternative to industrial testing, which is more cumbersome to set up.
Sorry, the comment form is closed at this time.