08 Jun How to match ingredients and productivity?
M. Verhoeven MSc (Zetadec, the Netherlands) and Dr. M. Thomas (Zetadec, the Netherlands and Wageningen university)
Ingredients are the basis of all animal feed. In times where alternative ingredients receive more and more attention, we should not forget to ask ourselves how ingredient properties affect the transition into actual feed. It is time to unravel the black box that is feed processing!
In the past decades, feed industry has been on a continuous quest for alternative ingredients: the use of animal protein sources has been reduced and partly replaced by plant protein sources such as soybean meal. The use of soybean meal, however, is known to be controversial because of various negative environmental impacts. As a result, numerous research institutes and feed factories are investigating alternative ingredients to be used in animal nutrition. These studies, however, often focus solely on nutritional aspects by investigating what the effect is of incorporating the ingredient in feed on animal performance. The technological process of transforming the ingredients into feed, better known as feed manufacturing, is often overlooked in these studies. Feed manufacturing is a relevant topic to consider, since differences in processing conditions and feed formulations will lead to pellets having different physical pellet quality. Physical pellet quality parameters such as hardness and durability have a great influence on factors such as storage and transport durability but, more importantly, on feed intake and thus animal performance. The current article will provide insights into the influence of ingredient on the processing of feed.
Zooming in: The effects of ingredient composition; components vs nutrients
To gain a better understanding of the effects of ingredients on feed processing parameters, we need to break down the ingredients and look into their composition. Carbohydrates, protein, and fat are three nutrients which are of great interest from a nutritional point of view, as these substances are used by animals to survive, grow, and reproduce. When we focus on how nutrients influence the productivity and physical quality of the feed, they are referred to as components.
Starch for example, a polymeric carbohydrate composed of a large number of glucose units, functions as a binding agent in pellets. To function as such, the so-called native or raw starch must combine with heat and water (which is given in the form of steam). This, in turn, alters the starch structure and allows reordering of the molecules. This process, termed gelatinization, can either take place during the feed manufacturing process (e.g. in the conditioner), or prior to it by including gelatinized starch in the feed mash. After gelatinization, the starch contributes to physical pellet quality through acting as both a binder and a lubricant, both gluing particles together and reducing the porosity, creating softer particles which are more easily deformable during pelleting. The pellet durability and hardness of pellets increases when a larger amount of gelatinized starch is included in the mixture.
Next to starch, proteins are also known to exhibit adhesive/binding forces. Protein structure can be denatured in the presence of heat and water, their structure is broken down, thereby changing the bioactivity of the protein. Protein and starch are known to interact in their effects on pellet durability and hardness, but their effects are not additive. There is a difference between the effects of adding raw protein versus denatured protein to either raw or pre-gelatinized starch on Holmen pellet durability, as is shown in Figure 1. Adding gelatinized starch into a formulation results in a higher pellet durability, compared to native starch. If we exchange denatured for raw protein, we can see that pellet durability increases. Pellet quality cannot solely be predicted from the component composition in a ration; the state of each component is also influencing final quality.
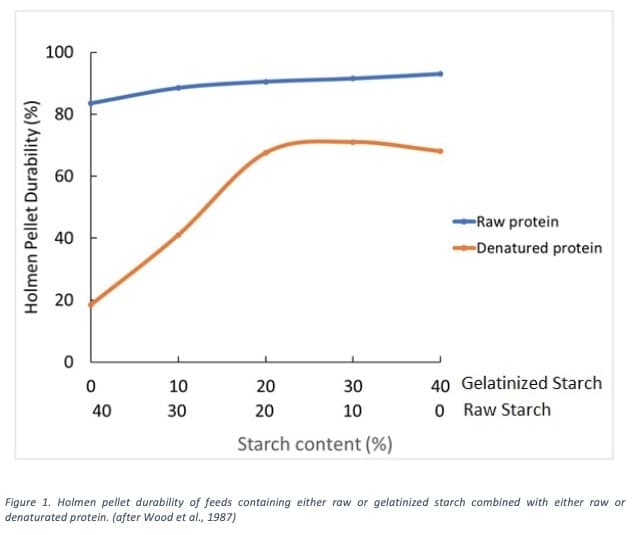
Even though raw protein results in better pellet quality, most protein rich feed ingredients that are used in the feed industry are thermally treated and therefore denatured, which does not contribute to good pellet quality (see Figure 1). Moreover, it should be noted that feed generally contains a greater proportion of starch than protein, implying the effect of protein on pellet quality is smaller than that of starch.
Fat, on the other hand, generally has a negative influence on pellet quality. This can be explained by fat’s hydrophobic nature: fat and water do not mix well, but water is required to initiate binding properties in both protein and starches. The effects of fat on mill efficiency and production rate are, however, positive. Fat or oil added into a ration acts as a lubricant, resulting in a decrease in energy needed to pelletize the diet.
The challenge: predicting physical quality of feed from its components
Even though looking at feed manufacturing from a nutrient point of view helps us to gain a better understanding of animal performance, we should also consider the effect of these components on the productivity and pellet quality when manufacturing feed.
Predicting the possible effect(s) of including certain ingredients includes an extra difficulty. Unprocessed, raw materials (such as corn, lupin and soybean) are not of constant nutritional composition either, being dependent on origin, cultivar and season of growth. In addition, (thermal) processing alters the state of the components, making it difficult to predict the combined effect of variability in nutrient composition and state of the components on physical quality of the pellets.
To conclude, the effects of ingredients on feed production can be predicted partly from their nutrient composition: a starch-rich feed mash will behave completely different during processing as compared to a fat-rich feed mash. Different ingredients are all composed of components in different ratios, and it is, therefore, more meaningful to consider the effect(s) of incorporating different components and their state in a formulation, rather than different ingredients. The main goal for feed manufacturers and researchers is now to gain more insight in how components in different states, rather than nutrients, behave and interact in different formulations and under different process conditions. State phase diagrams may allow us to gain these insights. State phase diagrams show how different processing conditions (e.g. temperature and moisture content) result in different states of components. Understanding these transitions will lead to better understanding of how the components react and interact with each other. This knowledge should aid in formulating diets that meet nutritional requirements without neglecting physical pellet quality.
References available on request
Sorry, the comment form is closed at this time.